但当前市面上的移栽机大多均为半自动移栽机,有很多弯腰、伸手的动作,在密集作业时,可能会有一天 8 小时的劳动时间,劳动强度非常大;随着农村经济的高速发展,作业人员数量逐渐减少,种植成本大大增加;并且,人工递苗和取苗的速度制约了移栽作业的效率。为了提高苗木移栽效率,用一款便捷高效的自动化栽植机构来代替繁重低效的人工栽植非常有必要。
1 自动苗木栽植机器人总体方案的设计
设计一种自动栽植机构,包括取苗定位机构、苗木存储机构以及栽植机构。设计其结构,并对其机构特点及动作要求进行深入分析,结合幼苗农艺夹持特性,对取苗末端执行器参数进行优化,分析其夹苗轨迹。
1.1 机械方案的设计
栽植设备的作用一般是从栽植设备中苗木存储机构中取得待栽植的苗木,然后通过轨迹规划将苗木栽植到土地中去。在此过程之中,种植处的种植深度也是栽植的一个重要条件,此设备需要精确的获得数据,以确保栽植目的的完成。
本文设计的自动苗木栽植机器人主要包括取苗定位机构、苗木存储机构以及栽植机构,取苗定位机构初步采用步进电机来提供动力,取苗末端执行器初步选择气缸来提供动力来夹苗。机械手部分进行栽植工作。总的来说,该机器人采用履带式移动平台+机械手驱动装置+末端执行器+栽植装置。并且自动栽植机构的末端执行器设计,调试适当的空间角度,保证其不会造成苗木损坏,尽量做到结构简单、尺寸较小、方便安装;自动栽植机构的运动轨迹应尽量合理、采用杆机构,易于实现;自动栽植机构的设计应符合农艺要求,在此基础上增加末端执行器的数量,从而提高取苗作业的工作效率。
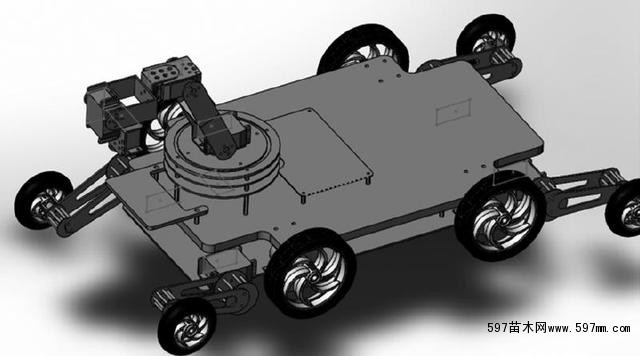
图 1 自动苗木栽植机器人
1.2 主要机构设计
1.2.1 取苗定位机构
取苗定位机构采用步进电机来提供动力。
步进电机是一个数模转换类控制电机,主要工作是将电脉冲转为角位移。从机构角度上来讲,步进电机主要为三种类型,分别是永磁式、混合式以及反应式步进电机。电机的控制源与机械运动转速都与脉冲离不开关系,每一个脉冲被电机捕捉到,电机的转子相应的转过一个步距角,同时电机的转速与脉冲频率呈现同比关系。
通过对步进电机的三种类型的性能之间对比,本次课题选用 HS 步进电机。课题中的高精度、小步距角等一些要求恰是 HS 步进电机所有的特点。因此,本课题选用两相四线的HS步进电机为设计研究目标。
1.2.2 栽植机构
栽植机构的设计其实主要包括取苗末端执行器与机械手部分的设计,其中取苗末端执行器选择气缸来提供动力夹苗。机械手顾名思义便是进行栽植。
末端执行器:在机械手尾部装有压缩棉花,以防破坏苗木活性;压土部分采用斜坡形式将土压实。整个种植苗木过程:爪手松开,等苗木完全处在土坑中时,斜坡面下压,填充穴孔,接下来向上举起斜坡面,离开穴盘,完成整个过程。全过程的动力源通过使用气缸装置获取。
气缸主要是驱动活塞进行往复运动,使得空气膨胀压缩,在能的形式上将压力能转变为动能,是一种常见的气动元件。本课题采用 TN10X125 号气缸,属于常见气缸中的行程气缸,其行程为 125mm。
机械手:机械手为机器人的主体,一方面在移栽过程中,已经能够精确的完成整个执行命令,另一方面也考虑到了在之后的发展中可添加其余指令空间。整个机械手的执行指令可以在电脑端或者控制器处下达。
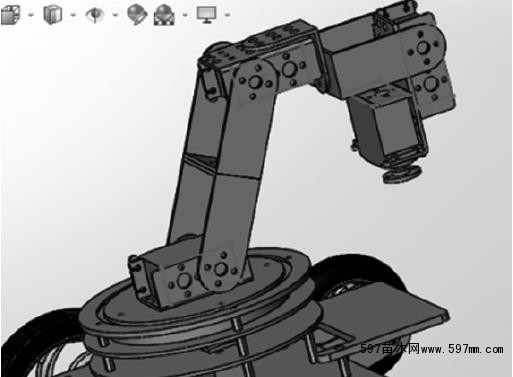
图 2 末端执行器和机械手
2 自动苗木栽植机器人控制方案设计
2.1 末端执行器参数优化
为了达到精准夹持以降低伤苗率,需要对末端执行器的杆件参数进行优化设计,实现特定角度的夹苗、放苗,研究末端执行器夹苗轨迹。
2.1.1 末端执行器建模
以图 3 所示的对称机构,建立相应的数学模型。将原点取为上固定处曲柄端,建立平面坐标系轴。点 A 连接曲柄滑块,为执行器 BB' 提供位移来源。苗针 EF 与连杆构件 BC 通过连杆 CD,以固定端 E 为端点,夹苗处 F 点,使 EF 进行旋转运动。
建立矢量方程:

将矢量方程化为解析形式,可以分别求解 A,B,C,D,E,F点轨迹。

图 3 末端执行器示意简图图 4 单侧末端执行器数学模型
2.1.2 末端执行器参数初步优化
在进行末端机构执行指令中,有几个重要的参数。一是苗木的转动角,二是它的中心距。这两个参数在整个行程中,就是夹取与移栽过程。因钵苗的基质受力、材质特性影响,夹取苗木的角度会在苗针通过存储机构过程中有所变化。同时,基质的受力过大,会使得钵体变形而导致散垛,因此也要考虑到中心距要超过在此条件下的最大受力(最大的变形量),在斜坡面压土过程后,为避免穴盘受到末端干扰,秒钟的中心距和夹持角也要满足不大于穴口的长度与不小于锥度两个要求。考虑到不同夹持位置所相应的苗株受压缩量与夹持角度的不同,通常我们都选取夹持基质发达的根部,即钵苗的中下部,这也是为了满足送苗过程中,保证苗株的活性不受到伤害。
通过末端夹持机构运动学的建模方程,将杆件 1OA,1AB,1BB,1B′C,1CD,1DE,1EF作为关键参数考察执行机构的夹持效果所受影响呈现为强耦合非线性。通过 VB 软件,对以上杆件参数进行优化整合。为获取穴口倾角度数与对应条件下基质所能达到的最大变形量且达到改变杆件各长度、固定端坐标位置、图像界面的图形这三个目的,以夹持角、移栽角、中心距等由e 点的坐标等因素输入得来的因素为程序参数与标准优化,且输出各个因素参数。
通过以上方式调节参数后,得到的满足精确夹持取苗的机构参数组合对应为 1OA=5mm,1AB=20mm,1BB=62mm,1B′ C=13mm,1CD=27mm,1DE=50mm,1EF=150mm,Xe=35mm。在此参数下,夹持角为 16°,夹苗中心距为 13mm。
2.2 末端执行器夹持动作轨迹分析
基于上述末端执行器各杆件参数,及固定参数。相应最佳夹持参数下中心矩为 9.9mm 和 77.9mm,夹持度为7.6°,放苗度为 1.2°。以输出的各参数为标准,通过 ADAMS 建立机构模型。通过控制杆在气缸为动力条件下带动苗针完成完整的单次行程的动作,得出中心距-气缸运动距离图形。中心距作为Y 轴参数,气缸运动距离作为 X 轴参数,如图 5。
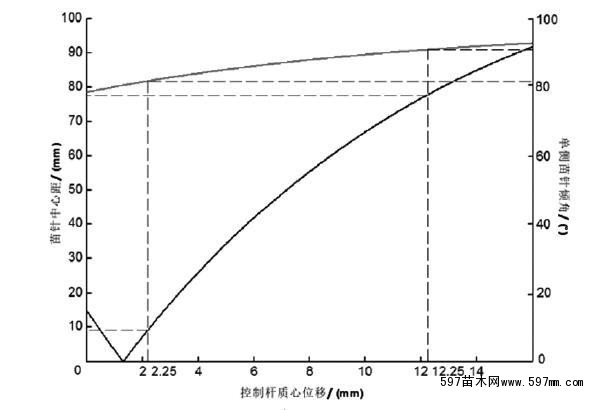
图 5 苗针轨迹参数-控制距离曲线图
选取位移距离 0-20mm,中心距 0-10mm。通过仿真所得曲线图,整个中心距在运动距离位移的增大过程中先降后升。在距离达到 2.25 与 12.25mm 时,中心距分别接近 10 与80mm,位移距离为 10mm 中心距范围在 69mm 内,基本运动符合预期,仿真分析与理论分析基本一致。
3 试验验证
3.1 试验目的及评价指标
考虑到取苗的定位控制与夹持控制对于整个末端机构的深度影响方面,这两种控制程序所构成的系统是本试验的主要内容。检测末端执行的定位精确程度,来判别是否满足运动控制定位的要求,最终以本试验得到的数据观察末端执行机构的取苗综合能力和苗株存活率,以便于末端控制系统的优化。
3.2 试验方案
末端执行机构控制系统以往复式间歇作为运动形式,其目的是将储存机构中苗木进行栽植,运动定位控制系统的控制精度直接影响末端执行机构的取苗效果。因此,本试验主要考核指标是末端执行机构定位控制的定位精度。
3.2.1 末端执行机构水平运动定位精度的研究
根据以上分析要求,主要分析机械手的定位过程的精度。将末端机构运行到苗株上 10cm 处,整个机构以水平端往复移动,操作模式采取单步运行。水平位移从 15cm 到 44cm,测试点分别采取 20、30、40cm 处。测量时其条件设定参数为2000HZ 脉冲值,25mm/s 的水平位移速度。测量工具取 syntek电子卡尺,由于其量程在 0-150mm 范围之内,因此在每一测试点的前 5cm 需要进行预先标定,在此次试验里,测量距离即是实际位移与标定的距离。原点选用水平位移的起始点,在每个位移点下以往返两次作一次测量,取到达苗株坑侧的位置,反复试验十次,最后得出十组数据。以两次数据之间的位置与往返精度,进行误差分析,总计得出每组 2 个位置误差与1 个往返重复精度误差。分析水平位移与其精度和重复定位精度关系。
3.2.2 末端执行机构升降定位精度的研究
根据水平运动精度的研究试验,将试验运动形式转变为升降运动,使用相同的测量工具与方式,测量时条件系数不变。升降运动从 4cm 到 6cm,以每 5cm 为测试的位移行程。原点选取为机械手升至的初始点,每次下降到测试位移的行程量时进行记录。最后分析十次下降的位移数据。
3.2.3 末端执行机构工作性能测试
调整初始位置,符合工作标准,末端执行机构工作于自动模式进行完整的取苗工作测试。PLC 输出脉冲 2000HZ,机械手水平行进速度 25mm/s。
3.3 试验结果与分析
试验台运行测试进行于 2020 年 3 月 26 日,测试得出预行测试方案数据。因栽植期不符合本地时期,缺少试验所需素材,考虑塑料泡沫基质与测量素材所需值接近,故进行代替测量,以保证试验顺利进行。
在本次定位控制实验过程中我们能够发现,游标卡尺其实很难对机构定位精度进行一个非常准确的检测,而在多次运行过程中,我们还能发现,其实测量误差才是定位精度有关数据误差的主要来源。在我们的实际运行过程中,由于机构震动或者人为等等不可控因素造成的测量基准的偏移很大,测量数据噪声也很大,这就不能作为精度测定的依据。
在末端执行机构工作性能测试中,存储机构并未受到机械手干涉,执行机构夹苗成功率远超预设,但出现夹取后苗针锁死在泡沫内部情况,考虑到泡沫与苗株生物特性差异,因此将此类情况排除在夹持依据之中。
4 结束语
设计了一种包括取苗定位机构、苗木存储机构以及栽植机构的自动苗木栽植机器人,其机械手臂在执行整个程序过程中,对于苗株的移植、栽种,穴口的处理和整个过程的定位都达到预期效果,苗木移植栽种的效率得到提升,同时还需要对定位方面的精确程度处理需作出进一步的调整。